WCU students triple face shield production
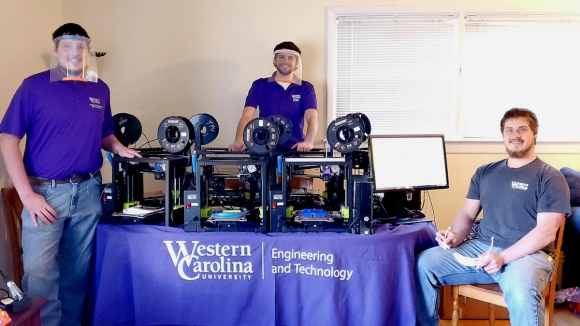
Students from Western Carolina University’s College of Engineering and Technology have checked out 3D printers from the university and are using them from home to help produce face shields for use by health care professionals during the global COVID-19 pandemic.
The addition of four students has enabled the College of Engineering and Technology to triple its capacity to build the visor portion of face shields using 3D printing to more than 350 per week, said Patrick Gardner, director of the Rapid Center, WCU’s research and development facility.
The student efforts are part of a community service initiative led by the College of Engineering and Technology to make face shields that are being delivered by WCU’s Center for Community Engagement and Service Learning to the medical community across Western North Carolina.
Gardner and other faculty and staff began building face shields earlier this month, with a maximum capacity of about 120 per week with one printer running 24 hours a day, seven days a week. The Rapid Center was shipping face shields to Stratasys, a manufacturer of 3D printers, which issued a call to businesses, industries and universities across the nation with 3D printers to participate in a nationwide consortium.
After those initial deliveries, the Rapid Center shifted its focus to regional hospitals, emergency responders and others on the frontlines in the global COVID-19 pandemic.
“It was clear that 120 shields per week would not meet the demands of our region, and that is when the students stepped up to assist,” Gardner said.
Related Items
Two students involved in the project are roommates who have converted their off-campus house in Cullowhee into a veritable 3D printing farm. For senior Brian Foster, an engineering technology major from Swannanoa, the work is more than just an effort to lend a helping hand in a time of crisis; it’s something that hits close to home.
“The real drive for me is my fiancé and family members who work as nurses in the health care industry,” Foster said. “I have heard the stories about the situations that our health care professionals are facing on a daily basis. I am working on this project because God gave me the skills and knowledge to be an engineer, and I want to use them to help in the fight against COVID-19.”
Anthony Mongold, a senior electrical and computer engineering technology major from Carthage, originally borrowed a 3D printer from the university to conduct material testing and help create user guides for the College of Engineering and Technology.
“However, once Dr. Gardner started this project, I was able to check out a second printer and switched to printing only the visors necessary to build the shields,” Mongold said. “Due to some of the properties of our available material early on, I modified the 3D model in order to increase its success rate. I also used my personal 3D printer to help prototype and design a visor that is printed in three pieces and can be assembled afterward.”
Based on that prototype, Mangold and Foster’s roommate Alexander Sapp, a senior electrical engineering major from Concord, fine-tuned the process, allowing them to use 12 university 3D printers too small to produce a full visor. “This maximized our potential output so that we can get as many supplies as possible to those who need it,” Mangold said.
The students say they are putting into real-world use many of the skills learned through their engineering and technology classes, including repairing and recalibrating printers when necessary.
“This project is no different than how a project would be carried out in industry. We work together on designing and updating designs using feedback we receive from local hospitals in order to improve our face shields,” said Foster. “This project has brought together some of the brightest and most dedicated individuals in the College of Engineering and Technology. Together I believe we are making a difference. If we can prevent even one health care professional from contracting COVID-19, then the project will be a success to me.”
“As an engineering student here at WCU, I was given the ability to learn how to use these amazing machines and to develop models for production,” Mangold said. “This one project alone has helped advance my 3D modeling expertise. As an electrical and computer engineering technology major, the real-world practice I get from repairing these printers is invaluable. The best part of being part of this team is knowing that we’re taking all of these printers that would just be sitting around collecting dust, and we’re using them to make a difference in the world. It may not be much, but in a crisis like this every little bit helps to save lives.”
Lindsey McGregor, a senior mechanical engineering major from Bryson City, also is using at-home 3D printing to help produce the face shields.
“What these students are doing is absolutely fantastic,” said Jeff Ray, dean of the College of Engineering and Technology. “WCU’s Rapid Center and College of Engineering and Technology are committed to the economic development, health and safety of our communities in Western North Carolina.”
For more information about the college, visit cet.wcu.edu.